Propose of this method statement is to describe the sequence of activities which will be followed to execute the steel structure fabrication works, including unloading of the raw materials and loading of fabricated materials to dispatch at project site.
Below is list of plant machinery and necessary equipment for doing the fabrication of steel structure and its elements.
The equipment engaged for works shall be checked and approved by plant and machinery department.
All equipment engaged in steel fabrication works shall be calibrated. List of equipment and calibration certificate of the same shall be provided to Employer’s engineers for records.
Machinery/Tools/Equipment engaged to carryout works are as follow:
- High Speed CNC H Beam Drilling Line
- CNC Band Sawing & line Cross Conveyor
- CNC Cutting Machine with Plasma Flame Cutting Machine
- High speed CNC Drilling Machine
- Floor Type Boring/Milling Machine
- ABW 2100 Beam welding Machine
- Automatic Shot Blasting Machine
- Paint Booth System
- Lifting Chains
- Lifting Clamps
- D-shackles
- Cutter/Hacksaw
- Pug Cutting Machine
- Welding Machine
- Grinding Machine
- All Hand Tools like Hammer, Chisel, Gas heating torch, Spirit level, measuring tape etc.
- Electrode Baking oven.
Roles and Responsibilities
Project Manager:
Ensure that all the equipment, tools and tackles required to execute the works according to approved construction Schedule are available in good condition and provide any additional equipment as required.
Ensure all the equipment/vehicles are handled by licensed / skilled operators.
Provide all necessary support to his construction team and ensure that the works are carried out as per the approved Method Statements/procedures.
Co-ordinate with site engineer, Surveyors, Safety Engineer, Quality Engineer, and frontline supervisors for safe & proper execution of the steel structure fabrication works.
Ensure that, checked levels shall be entered in level books as per the approved formats & requirements on daily basis.
Ensure that levels are jointly being signed by the contractor and Client representative
Continuously check the progress of works as per schedule / programs.
Ensure Client approval on all checklists / permission as and when required.
Project Site Engineer Job Description
Understanding the drawings prior to start of work and all details are provided to execute the work. If not, then take clarification from Client.
Compliance to EHS and QA/QC requirements prior to commencement of work.
Engaging workmen in work according to plan.
Cross checking the activities intermittently during day’s work and ensuring the activity is done within tolerance limits.
Mobilizing the materials required for work prior to start of work. Preparing safe to work card for all activities and giving PEP talk based on the safe to start work card as part of the work instruction to workmen working under him highlighting the risk involved in the task.
To ensure safety of workmen working in his area. To ensure proper working platform with access to keep materials.
Ensure all working and checking tools are available at site with working team before start of work.
To ensure proper housekeeping at site at the end of day’s work.
Understanding EHS requirements of project from EHS plan, EHS management systems, EHS Manual & following the same in execution of work.
Marking legibly grid reference/ Date of construction.
Ensuring implementation of proper work methodology for all activities.
Preparation of all checklists and certification of works from Client.
Co-ordinate with site engineers and ensure that the survey works are carried out according to the latest drawing.
Preparation of all checklists and certification of works from Client.
Ensure that all construction equipment and vehicles are inspected and cleared by P&M and EHS department.
QA/QC Quality Engineer
Communicating with all site staff about the Quality requirements as per QMS.
Shall ensure all inspections and tests are conducted as per approved Inspection and Test Plan.
Ensure only approved materials incorporated in works.
Make sure that Raw Material is as per approved make and traceability maintained.
Ensure required training and induction provided to all workers/supervisors.
Make sure fabrication procedure is as per approved Fabrication Method Statement.
Ensure all testing is performed, witnessed and verified by Inspection agency.
Surveyor
To establish bench marks from agreed reference points, provide required setting out and line and level markings and follow up regular checks.
Co-ordinate with site engineers and ensure that the survey works are carried out according to the latest drawing.
Maintain survey details and reports.
Duties of Health & Safety In charge
Shall inspect in maintaining safe working environment & conditions and compliance to Project EHS Plan. Shall facilitate in EHS Risk analysis and ensure required preventative measures.
Ensure awareness about all works procedures and risk involve in it and all necessary precautions has been taken before commencement of fabrication works.
Make sure all inductions and trainings are provided to workman related to safety.
Identify potentially unsafe acts, areas and practice and educate people
Monitor EHS practices, persuade to minimize non compliance
Report incidents beyond control and unsafe occurrences. Issue stop work notice for unsafe work.
Investigate unsafe occurrences and initiate preventive steps.
Discuss near miss accidents with staff and workmen
Conduct safety training programs and celebrations
Review Health & Environment related aspects as per the norms.
Access and Egress Requirements
Proper access and egress will be ensured before and till completion of steel structure work.
Temporary signage will be provided at access and egress.
Approaches and exits shall be clearly defined by barricades and warning/caution signs.
Proper illumination and ventilation as per SH&E Plan/ Manufacture recommendation will be ensured at site during work and shall be monitored periodically.
Necessary safety precautions will be taken for works at heights.
Emergency Arrangements
Emergency assembly point shall be provided near work place.
Round the clock ambulance and first aider should be available at the site with the required equipment’s and accessories.
Fire extinguisher shall be provided near the work place.
Storage and Staking of Materials
Stacking of all steel plates shall be proper, size and section wise.
Material shall not be stacked directly on earth. It should be at-least 300mm above from the ground and to be kept on wooden planks.
It shall be stored in open to atmospheres, either it’s in shaded area or shall be covered properly with Tarpaulin sheets.
Rolled section shall be stacked in such a way that edges of section not damaged.
Height of stack shall not be exceed from 2 meters.
At field/shop, electrodes will be kept in portable ovens.
HSE Requirements During Steel Fabrication Works
All the manpower involved in the job shall wear appropriate personal Protection equipment’s like Helmet, Safety shoe, gloves, nose masks and safety belt wherever required.
Proper approach to the work spot, and proper illumination shall be maintained.
Ensure that height work permit is obtained to start that job and life line provision available if required.
All precautions shall be taken care for loading, unloading and shifting of materials.
Housekeeping shall be done and all paint marks and splashes on surrounding surfaces will be cleaned after completion of work.
Ensure that relevant risk assessment is available with the engineer during activity.
General Requirements for Fabrication Workshop and Works
Location of all fabrication yard including working area shall be provided to Employer’s Engineer separately.
Site condition of working area shall be as per industrial norms and suits to project nature and quantum of works.
All steel work before and after fabrication shall be straight and free from twist.
All component parts shall be assembled in such a manner that they are neither twisted nor otherwise damaged, and forcible connection to fit the members together shall not be used.
Load-bearing connections containing more than one type of fastening shall not be used unless specified or approved by the Inspector.
Training for all potential safety hazards like loading/unloading, lifting/shifting/electrical safety, impact of corrosion and water logging etc. shall be provided to all workman.
Sequence of Work For Steel Fabrication Works
Lifting and shifting of Structural Steel:
Fabricator stores to unload the material being supplied by the main contractor at designated location at fabricator’s storage yard grade-wise, thickness wise etc.
Everyone involved in the unloading of materials must take all necessary safety precautions to reduce the risk of incidents.
In particular, unloading should never be carried out unless all the risks have been assessed, even if this results in a delay.
Such delays can be avoided through proper planning.
Structural Steel shall be new and shall be well and cleanly rolled to the dimensions, sections and weights specified.
It shall be sound and free from cracks, surface flaws, laminations and other defects and shall be finished in a workmanlike manner.
Structural Steel will be unloaded as per size (Thickness) and properly stacked by using wooden sleepers properly placed so that at the time of cutting sleepers will not come under the cutting zone to avoid additional handling of material during cutting.
Crane/Hydra will be placed between the cutting bed and the assembly platform so that it can be operated from the same area for both the platform to reduce the material handling time.
Lifting Equipment
All lifting equipment like lifting chains, D-shackles, Lifting clamps will be as per capacity with proper safety norms and proper test certificate from the manufacturer/load test approved by authorised third parties.
The Lifting Operations and Lifting equipment required ensuring that all operations, such as unloading/loading/ handling from one area to other area of steel, are properly planned by a competent person, appropriately supervised and carried out in a safe manner.
Lifting equipment will be used to be suitable for the use to which it is being put, properly maintained, marked with its safe working load, and periodically thoroughly examined and inspected before start of unloading /loading/handling of plates.
Welder Qualification Approval and Traceability
Welders will be qualified as per approved WPS/PQR.
WPS and PQR shall be submitted separately to Employer’s Engineer for approval.
After approval of WPS, test coupon will be prepared (duly witnessed by Employer’s Engineer/Inspector) as per approved WPS and test coupon will be send to approved third party laboratory for testing.
If the test coupon pass in all specified parameters, PQR will be freeze.
On the basis of approved PQR, welder qualification test shall be performed.
Qualified welders shall be provided unique welder ID
List of qualified welders along with respective welder ID number shall be provided to Employer’s Engineer to review and records.
Welder traceability can be verified fit-up and weld visual report and as per approved WPS/PQR.
Fabrication Procedure including steel marking and surface preparation
Suitable platform is required for assembly and Welding.
Due to higher thickness of plates, Distortion will take place while continuous welding process will going on to arrest all the distortion its very essential to make suitable heavy support platform has to be placed at 1meter distance to prevent distortion due to weld heat inputs so as to keep plates in perfect level and sequence shall be carried out before start the welding
Before start of welding, the entire member is locked properly by using extra support to avoid distortion.
After completion of welding, when the welded members cool down in normal/room temperature the extra support will be removed.
For fit up of every new member, cutting edges of the web will be removed and the fabrication platform needs to be cleaned properly by removing all the spatters/slag/previous welding spot.
Cutting& Marking
Raw materials shall be marked and cut to size by shearing, saw cutting, flame or plasma cutting and include the allowances such as cutting, grinding.
Cutting Allowances shall be as follows:
1) Up to 6 mm: 2 mm
2) For 6-25 mm: 3 mm
3) For 25-63 mm: 4 mm
4) For 75-150 mm: 6-8 mm
Flame cut edges shall be cleaned to remove slag.
Uneven edges shall be dressed by grinding.
Gas cuts shall be smooth and regular in contour.
Cutting of plates by pug machine needs skilled and experienced operators to maintain proper cutting edge. Also after one cut the next cut will be started in other side of the plate to avoid distortion in cutting zone.
Marking on steel shall be done in accordance of shop drawing and cutting plan.
Code of marking over fabricated member shall be as follows:
Drawing. No. / Mark No. / Part No. / Weight / Heat No.
This marking on members shall be done by hard punch.
Every separate member shall be plainly and permanently marked with paint to show position and direction as necessary for each identification and correct placing.
Loose pieces of connection shall be attached to their respective members.
Fit Out of assembly/sub-assemblies
a) Fitting shall be carried out after ensuring removal of burrs, notches, grinding of edges wherever required.
b) Identification markings for mark no., drawing no. and other shall be carried out as per the drawing/specification/approved QAP.
c) After completion of the fit out, Production shall check the job/assy./sub-assembly for completeness, physical condition to ensure absence of surface defects. Production will also record the name of the fitter(s) for feedback, improvement and skill level assessment.
d) IQC-Fit Up shall carry out inspection as per the drawing (drawing should have good for manufacturing stamping by PPC/PMG- to ensure that it is pertinent issue of the drawing). IQC shall prepare dimensional report and record dimensions, orientation of the child parts, correct weld preparation etc.
e) After completion of rectification, assembly/sub-assembly shall be cleared/moved to welding section. Welding supervisor shall carry out welding using qualified welders and the procedures which are appropriate to achieve desired welding quality.
Punching, Drilling and Reaming:
For Grade 4.6 bolts, holes in material up to 16mm may be punched, drilled full size or sub punched 3mm undersize and reamed to size.
Punching is not permitted in plates thicker than 16mm.
For Grade 8.8/10.9 bolts, holes must not be punched.
The hole diameter shall be 2mm larger than the bolt diameter for bolts not exceeding 24mm and not more than 3mm larger for greater diameter bolts.
Holes in base plates shall not be more than 6mm larger than anchor bolt.
A special oversize 4mm minimum thick washer shall be provided with these oversize holes or as specified in approved drawings.
Pre-heating:
Fit-ups of members will be carried out by qualified fitters under the supervision of Fit-up supervisors as per ITP/QAP/TS/Drawings.
There will be inspection by QC team as per ITP/QAP/TS/Drawings and after clearance welding will be started.
Preheat and Interpass Temperatures:
Parts to be welded shall be preheated by means of gas flames, or other means to bring to the specified preheat temperature the full thickness of the base metal for a distance equal to the thickness of the part being welded, but not less than 75mm from the point of welding.
Welding preheat temperatures shall be in accordance with AWS D1.1 and checked by thermal chalk or Temperature Gun.
The root run will be made by GMAW/FCAW for full fusion and checked soundness of weld by NDT make sure that there is no defect in the root.
After that, SAW will be used for filling the groove in multi-layer. In multi-layer welding slags, spatter, other impurities etc. on each completed weld shall be removed prior to the start of next layer.
For pre heating of long section, series of burners fitted in a suitable frame shall be used to maintain regular heating in total area at a time. LPG will be used as fuel for heating burner.
Thermal chalk or temperature Gun will be used to check the required temperature when heating process is going on.
WPS and PQR will be submitted for approval for following welding processes:
SMAW
GMAW
SMAW + SAW
Removal of Slags:
All slag, scale and other inclusions shall be removed and the adjacent metal brushed clean not only from the edges to be welded, but also from each pass or layer before the deposition of subsequent passes or layers.
This requirement shall apply not only to successive layers but also to successive beads and to the crater area when welding is resumed after any interruption.
The steelwork at welded joints shall not be painted or otherwise treated externally until the joints have been completed, slag, spatter, rust, scale, oil and dirt have been removed, the surface has been prepared as specified under “Corrosion Protection”, and the joint has been inspected and approved by the Inspector.
Blasting
The cleared jobs shall be moved to the blasting machine/manual blasting depending upon the size of the jobs.
Blasting shall be carried out and the parameters like time of blasting, finish achieved, visual check for completeness etc. shall be done by Blasting operator/supervisor in the register.
IQC Welding shall carry out one more check at this stage and ensure that the jobs is clear of scale, rust, profile and finish is satisfactory, any leftover welding, grinding, burrs, notches are taken care of before giving clearance for primer/painting.
This inspection shall be completed in 10-20 minutes of time to allow adequate time for primer application of the job.
IQC-Blasting area will put up a green sticker ÓK’ on the job and hand over the part mark list to the painting/blasting supervisor.
Painting supervisor will only move such jobs to painting area for primer application which has OK sticker and as per the cleared part mark list.
Non-conforming jobs list shall be provided to Head Operations for getting these attended, reworked.
These shall be re-inspected by IQC before these are moved to the paining area and accompany the cleared part mark list as well as identified sticker.
Painting, metalizing, stencilling and Identification Marking
Painting supervisor shall ensure that primer coating is done within 4 hours during raining days and within 4-6 hours on other days.
Painting supervisor shall maintain project wise record of primer, MIO and final coat paint opening stock, paint drawn during the shift and the closing stock.
In case, paint is required to be issued from Stores, Painting supervisor shall fill up the requisition and get it signed from and update records.
Paint supervisor shall also monitor paint mixing and its right proportion, quantity mixed, pot life for cutting down on wastage.
He will also maintain the part mark list along with drawing no and shall provide to calculate surface area and monitoring of the Paint Loss Factor’’
For the outsourced jobs, the concerned planning Engineer will maintain the above records of paint consumed, day wise, sub-con wise along with list of parts and surface area painted (separately for primer, MIO and final coat) to calculate Paint Loss factor and generation of MIRs.
Record of temperature, humidity (dry and wet bulb temp) shall be recorded at least 2 times in a shift, along with curing time given to each part mark by the Paint Supervisor.
WFT shall be checked by the concerned painter to control the process for final painting and DFT.
Stencilling and marking shall be completed and offered to IQC.
IQC will check for visual defects, paint thickness, DFT etc. and shall co-ordinate with client for clearance.
The list of the cleared jobs shall be provided to Paint shop as well as Logistics team to shift and plan for dispatch.
Bed area cleaning and final touch up shall be done by the Logistics Team and PDI shall be done by IQC- Paint & Logistics prior to dispatch.
Logistics will not dispatch without PDI clearance and shall ensure proper loading, lashing, rubberized padding to ensure safe and quality transportation.
Visual Management:
Stickers for Hold/OK/PDI processes, which provides in-situ communication to the stakeholders the job’s status.
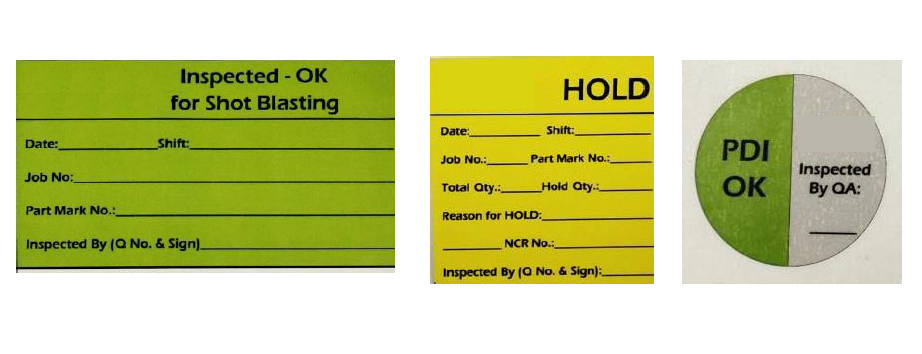
Inspection Requirements:
The Testing Agency/Inspector shall carry out all the shop inspections, non-destructive or destructive testing specified herein, review all test certificates and materials, undertake full-time inspections of the fabrication works on site, supervise welder’s qualification tests, inspect and test surface.
The Testing Agency/Inspector shall submit certificates for the various sections of the work directly to the Employer or Engineer’s Representative.
Ensure necessary testing/checking is done as per approved ITP. Daily records of quality checks shall be maintained.
All items shall be suitably packed in case these are to be dispatched from the fabrication shop to actual site of erection so that any damages/distortion can be avoided during transit. If necessary projected parts shall be temporarily braced to avoid warping during transit.
Following inspection offer formats cum checklists will be implemented:
Incoming Raw Material Inspection Report
Fit up Inspection Report
Welding Inspection Report
NDT Reports
Surface Preparation & Painting Inspection Report
Pre-Dispatch Inspection Report
Discover more from Project Management 123
Subscribe to get the latest posts sent to your email.