In order to ensure quality in all aspects of the construction site, close watch of subcontractors’ operations is no doubt compulsory.
Every contractor shall establish and document an appraisal system to verify their sub contractor’s implementation of and conformance to the project quality plan and contract technical specification requirements.
The appraisal shall cover all the quality-affecting activities for construction, as well as laboratories and shall be applicable to the onsite and offsite locations, including all subcontractors.
The Contractor shall deploy experienced and capable subcontractors in the project. Their works shall be inspected by client’s supervising personnel and QC Engineers. Their activities will be duly inspected per the field inspection checklists.
Inspection Acceptance Procedure
Construction acceptance criteria for materials qualifications, inspection, and testing are established by technical specifications. Criteria for materials and equipment have been set by clients QA Staff in accordance with the applicable codes and standards, and by manufacturers’ recommendations.
Contractor submittals are to document conformance with acceptance criteria as detailed in their PQP (control, verification, and acceptance inspection and testing plan ITP).
The contractor QC control, verification, and acceptance testing plans set out the QC inspections and testing for implementation of each technical specification applicable to the contractor’s scope of work.
The inspection and test plans ITP’s will cover the type, test standard, frequency, control requirements, and assigned responsibility for inspections and tests. The Client will review and approve these plans as part of the contractor QCP submittals.
General construction Inspection and Verification Requirements
Contractors shall perform the inspections and tests as prescribed in the technical specifications for the Contract.
QA inspection and testing will be used to verify the adequacy and effectiveness of the contractor QC program.
The QA inspection and testing frequency will be at the discretion of the consultant based on results of QC tests, evaluation of daily reports, audits of the QC program and verification testing conducted by client, consultant and third party testing firm.
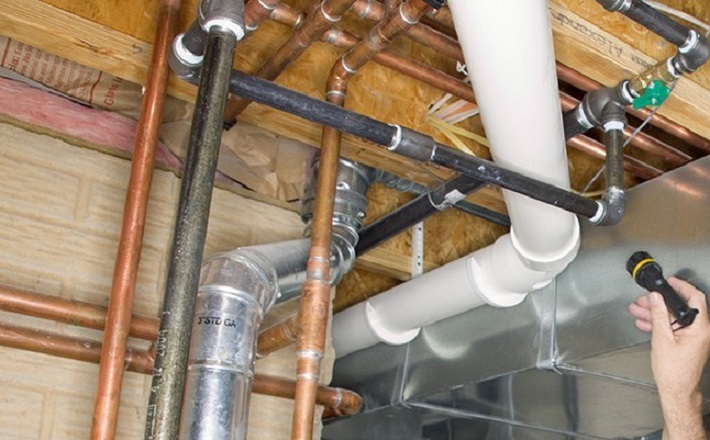
Should information become available that indicates a potential problem, client or their representative will review in detail all pertinent information and order additional verification testing if necessary.
Contractor QC control, verification, and acceptance testing plans set out the contractor’s specific QC testing and inspection pursuant to Specification and the relevant design specification.
Inspection and Testing Plan
Materials qualification testing will be done prior to construction to verify that the materials comply with requirements of the specifications.
The contractor will obtain representative samples of the materials designated as the proposed source of the materials. Test samples will be sent by the contractor to the Testing Laboratory.
The Testing Laboratory will report all test results for determination of material meeting the acceptance criteria.
If determined that the characteristics of the material being used differ from the material initially tested, client’s QA staff will direct the contractor to repeat the qualification testing.
If the new material qualification test results meet the criteria of the technical specification, the new materials may be used for the work; otherwise, previously approved materials must be used or other acceptable materials must be sampled and tested as noted above prior to incorporating into the work.
Inspection Discrepancy / Non Conformity Procedure
This section provides procedures for tracking construction deficiencies (non compliance) from identification through acceptable corrective action. It defines the controls and related responsibilities and authorities for dealing with non compliant/non conforming works or services.
When material, performed work, or installation is found deficient, QA Staff shall ensure that the non-conforming material, work, or installation is identified and controlled to prevent unintended use or delivery.
Client will notify the contractor of any noncompliance with any of the foregoing requirements. The contractor shall, after receipt of such notice, immediately take corrective action.
Minor deficiencies
Minor deficiencies noted during test or inspection are verbally reported to the contractor’s representative and noted on the daily construction report.
Ideally, such minor deficiencies can be corrected on the spot by agreement with the contractor’s supervisor.
Non Conformance’s
Non-conformances are major deviations from the contract requirement and/or accepted standard of quality, which is formally documented for corrective action by QA Staff shall follow up on the Non-conformances as required to verify that corrective action has been completed by the contractor.
Implementation of Assessment Procedure
The contractor shall establish and document an appraisal system to verify their or their sub contractor’s implementation of and conformance to the QCP and contract technical specification requirements.
The assessment system shall be used to make a determination regarding the effectiveness of the QC system.
The contractor’s auditing shall be planned, performed and documented in accordance with written instructions, procedures or checks to be included in the QCP.
The audit scope, frequency and methods shall be defined in the QCP. All non-conformance conditions identified during the audit shall be re-audited to verify the corrective actions taken by the appropriate organization were effective.
Inspection Program
The contractor shall establish a program for inspection of activities affecting quality and shall cover all construction site and laboratory operations, including both onsite and offsite operations.
Inspections shall be performed to verify compliance with documented instructions, drawings, procedures, and specifications as required by the contract.
All inspections shall be documented by the contractor and sub contractors.
A four-phase inspection program shall be followed for each definable feature of the work. The four phases of inspection shall be carried out following the Quality Inspection Report are:
Stage 1: Preparatory Inspection
The contractor’s QC Manager and the QA Staff perform preparatory inspections prior to beginning any work on any definable feature of the work.
- Ensure that preparatory inspections include a review of contract requirements.
- Ensure that all materials and /or equipment have been tested, submitted, and approved.
- Ensure that provisions have been made to provide required testing.
- Examine work area to ascertain that all preliminary work has been completed.
- Examine materials, equipment, and samples to ensure that they conform to approved shop drawings or submittal data, that all materials and/or equipment are on hand, and that all monitoring and measuring equipment is properly calibrated and in proper working condition.
- Record preparatory inspections in the contractor’s QC documentation
Stage 2: Initial Inspection
The contractor and client’s QA Staff performs an initial inspection as soon as a representative portion of the particular feature of work has been accomplished.
- Examine the quality of workmanship.
- Review control testing for compliance with contract requirements.
- Review dimensional aspects of the work.
- Record initial inspections in the contractor’s QC documentation
Stage 3: Follow-Up Inspection
The contractor and QA Staff perform follow-up inspections daily.
- Ensure continuing compliance with Contract requirements.
- Ensure continuing compliance with control testing until completion of particular feature of work.
- Contractor CQM records follow-up inspection in daily QC reports.
- Conduct final follow-up inspections and correct test deficiencies prior to the addition of new features of work.
Stage 4: Completion Inspection
The contractor and QA Staff perform a completion inspection of the work.
- Develop a “punch list” of items that do not conform to the approved plans and specifications.
- Include the punch list in the construction QC documentation that includes the estimated date by which the deficiencies will be corrected.
- Perform a second completion inspection after punch list items have been completed and client has been notified by the contractor.
The daily inspection reports shall identify inspections conducted, results of inspections, location and nature of defects found, causes for rejection, and remedial or corrective action taken or proposed.
Additional Quality Inspections
Additional QA inspections may include inspection of third-party lab testing facilities, fabrication facilities, and suppliers. Other inspections outside of the four-phase program described above will be ordered or performed by client to verify compliance with building code and standards.
These inspections shall be performed and conducted at various points of construction that would typically require code compliance inspections.
When deficiencies are discovered during the four-phase or other inspection processes, focused inspection shall be considered by client.
When material, performed work, or installation is found on the basis of focused inspections to be deficient and/or does not meet the project specifications, the contractor will assure deficiency correction is implemented.
Discover more from Project Management 123
Subscribe to get the latest posts sent to your email.